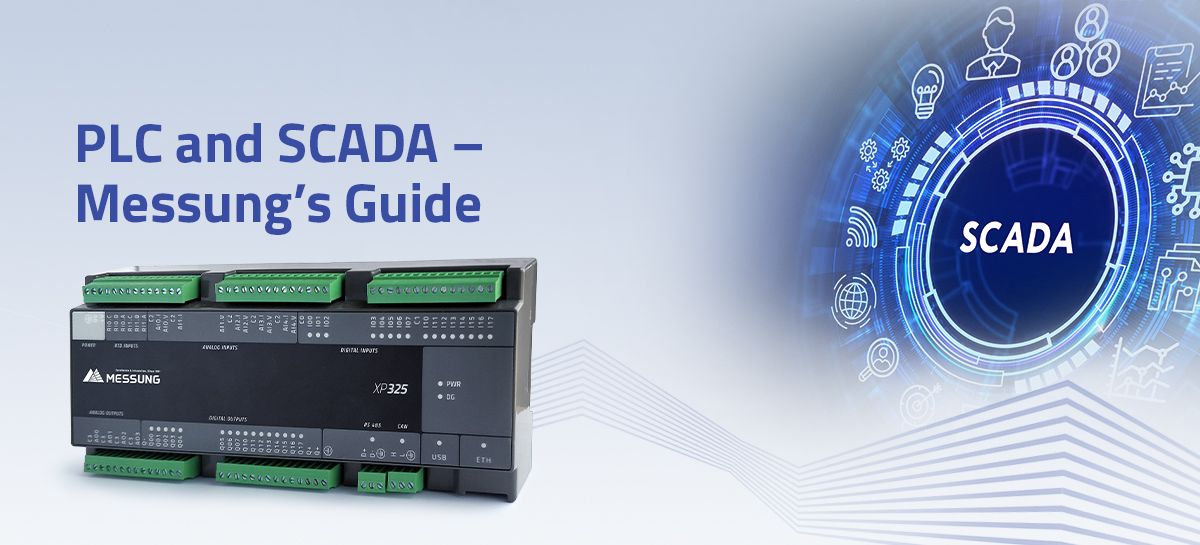
PLCs and SCADA systems are both used to control industrial process automation. PLCs, or programmable logic controllers, are typically used for more simple applications, while SCADA or supervisory control and data acquisition, systems are used for more complex processes. Both types of systems use sensors to collect data about the process and then use that data to control actuators to make adjustments to the process. PLCs are typically used in manufacturing applications, while SCADA systems are often used in power plants and other industrial facilities.
PLCs are used in a wide range of industries, from automotive manufacturing to food processing. SCADA systems are used in industries such as energy and water management. Both PLCs and SCADA systems can be used to monitor and control processes remotely. PLCs use a variety of input and output devices to interact with the process, while SCADA systems use remote terminals and computers to monitor and control the process. PLCs can be programmed to perform a wide range of tasks, while SCADA systems typically provide a higher level of control over the process.
PLC and SCADA systems are crucial to automation companies and industries that need automated processes to streamline their business. Both types of systems can be used together to provide a comprehensive solution for controlling and monitoring an industrial process.
1. Difference Between PLC And SCADA
Both PLC and SCADA systems are capable of gathering data, but there are some key differences between the two. PLCs, or programmable logic controllers, are designed to handle a specific process or task. They use sensors and input devices to gather data and then use that data to control outputs. SCADA stands for supervisory control and data acquisition and is designed for monitoring and controlling large-scale processes. They often include features such as data logging, trending, and reporting. In addition, SCADA systems can be used to control multiple processes at once. As a result, they are often used in industries such as manufacturing, oil and gas, and utilities.
PLC stands for Programmable Logic Controller and is typically more rugged and can operate in harsher environments than SCADA systems. They also tend to be less expensive and easier to program than SCADA systems. However, SCADA systems offer more flexibility and functionality than PLCs, making them the preferred choice for more complex applications. In addition, SCADA systems can be connected to a network of computers, allowing for remote monitoring and control.
2. When to use PLC and when to use SCADA
Both PLC and SCADA have their advantages and disadvantages, so it’s important to choose the right system for your needs. PLC systems are typically used for simple applications that don’t require a lot of data processing or analysis. They’re also relatively easy to program and maintain. However, PLCs can be more expensive than SCADA systems, and they’re not well suited for complex applications. SCADA systems, on the other hand, are designed for more complex process control applications. They can handle large amounts of data, and they provide powerful tools for data analysis and process optimization. However, SCADA systems can be more difficult to program and maintain than PLCs. In general, PLCs are best for simple applications while SCADA systems are better suited for complex applications.
PLCs can be programmed to carry out a variety of tasks, and they’re often used in manufacturing or heavy industry. SCADA systems, on the other hand, can gather data from various sources and then display that data in an easy-to-understand way. While PLCs are more versatile, SCADA systems are often easier to use and implement. So when choosing between the two, it’s important to consider the specific needs of your application.
3. What Are SCADA Systems?
SCADA systems are computer-based systems that are used to control and monitor industrial processes. Let us look at the components of SCADA for a better understanding of what constitutes it. SCADA systems typically consist of three main components: a human-machine interface (HMI), a remote terminal unit (RTU), and a central processing unit (CPU). The HMI is used to display information about the system’s status and to allow operators to issue commands. The RTU is responsible for collecting data from sensors and actuators and sending it to the CPU. The CPU is the brains of the operation, using the collected data to make decisions and issuing commands to the RTU. Together, these three components form the basis of a SCADA system.
While SCADA is often used in electric power plants and water treatment facilities, they can also be found in manufacturing plants and oil refineries. They can be used to control a variety of different processes, including the production line, the distribution of electricity, and the monitoring of environmental conditions. SCADA systems are often considered to be critical infrastructure for industrial automatics as they can have a significant impact on public safety and the economy. As a result, SCADA systems are subject to strict security measures, and any changes to these systems must be carefully planned and implemented.
4. How does SCADA Systems Work?
Simple Control and Data Acquisition (SCADA) systems typically consist of a central computer or server, which is used to collect data from a network of remote devices. The remote devices can include everything from sensors and controllers to pumps and valves. In recent years, SCADA systems have become increasingly complex, incorporating cutting-edge technologies such as wireless networking and web-based interfaces. Despite their complexity, SCADA systems still perform the same basic function: they provide a means of monitoring and controlling equipment and processes from a central location.
SCADA systems are used in a variety of industries, including water and waste management, power generation and distribution, and manufacturing. While each SCADA system is unique, they all share certain basic components. These include controllers, which act as the brains of the system; input/output devices, which allow the system to interact with the outside world; and communication networks, which connect the various components of the system. In operation, data from the field devices is transmitted to the controllers, which then use this information to make decisions about how to operate the process. The controllers then transmit commands back to the field devices, which carry out these instructions. By monitoring and controlling industrial processes in this way, SCADA systems help to ensure that they are operating safely and efficiently.
5. SCADA Programming
SCADA programming is the process of developing and maintaining software for SCADA systems. The SCADA program software is typically used to monitor and control large-scale processes or systems, such as power plants or water treatment facilities. In order to be effective, SCADA programming must be designed around the specific needs of the equipment and system being controlled. As a result, SCADA programmers must have a detailed understanding of both the software and the underlying hardware. Once the software has been configured, it can be used to automate various tasks, such as monitoring process data, issuing alarms, or controlling machine operations. By streamlining these tasks, SCADA programming can help to improve efficiency and safety in industrial settings.
SCADA programming code is typically written in a high-level programming language such as C++ or Java. In order to create this code, programmers must have a strong understanding of the SCADA system architecture and the specific hardware that will be used. Once the code has been written, it must be tested thoroughly to ensure that it works correctly. Only after the code has been verified as working correctly should it be deployed to the production environment. By following these steps, programmers can ensure that their SCADA code is reliable and effective.
6. Which one is better for your business: PLC or SCADA?
To decide which automation system is suitable for your business, it is important to understand the key differences between PLCs and SCADA systems. To repeat what we discussed earlier, PLCs are typically used in manufacturing applications, where they can be programmed to automate repetitive tasks. SCADA systems, on the other hand, are supervisory control and data acquisition systems.
PLCs can be used to control a wide variety of industrial equipment, from lathes and conveyor belts to pumps and motors. SCADA systems, on the other hand, are computer-aided software programs that give operators real-time visibility into the status of equipment and processes. While both PLCs and SCADA systems have their advantages, choosing the right one for your business depends on a number of factors. In general, SCADA systems are more complex than PLCs and offer more features and functionality. However, they also tend to be more expensive. When deciding which system is right for your business, it’s important to consider your specific needs and budget. If you’re looking for a simple solution that can be easily programmed to automate repetitive tasks, then a PLC may be the way to go. However, if you need a more robust system that can handle complex processes and provide detailed data tracking and analysis, then a SCADA system is probably a better choice.
No matter which system you choose, it’s important to partner with a reputable provider who can help you select the right solution for your needs. If you are unable to determine which automation system goes best with your business, Messung’s expert guidance can help you take the right decision. Messung’s systems are reliable and easy to use and backed by a team of professionals who will help you get up and running quickly. Choose Messung for all your automation needs and experience the difference.