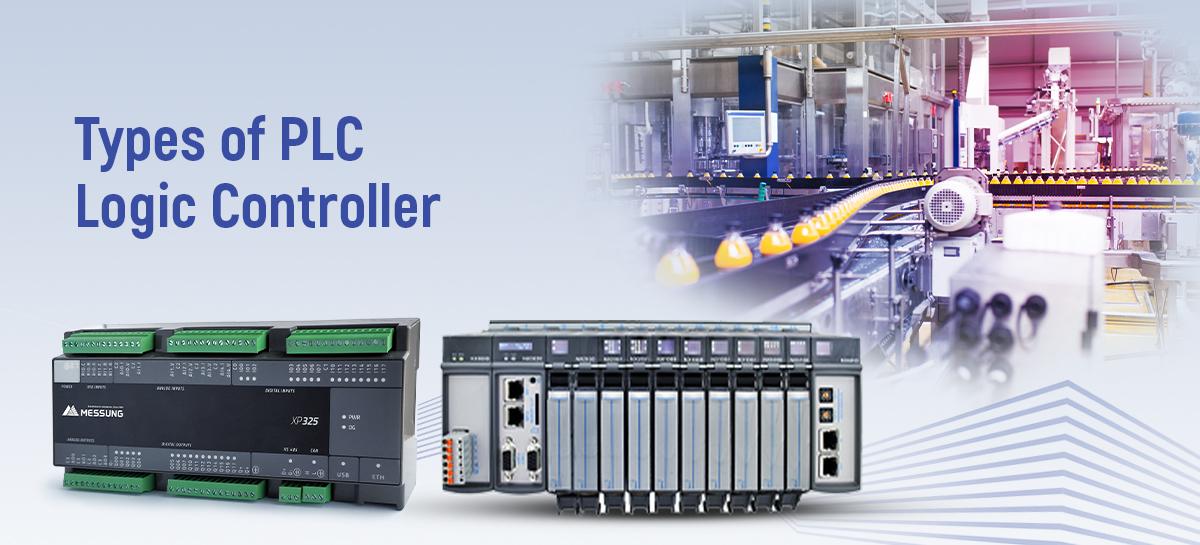
The industrial sector has seen a rise in the adoption of PLC industrial automation in recent years. PLCs (Programmable Logic Controllers) are devices that can be programmed to automatically carry out certain tasks, such as monitoring and controlling machinery. PLC automation offers several advantages over traditional methods of industrial automation. For example, PLCs are more efficient and less expensive to maintain than older technologies. In addition, PLCs offer greater flexibility and functionality than older systems, making them well-suited to the ever-changing needs of the modern industrial sector. As the benefits of PLCs become more widely known, their use will likely continue to grow in the years to come.
Importance of PLC
A PLC, or Programmable Logic Controller, is a central part of an industrial automation system. It is a computer designed to oversee and manage a wide range of industrial processes, from simple machines to complex production lines. PLCs can be connected to networks of sensors and controllers, allowing them to operate autonomously or in coordination with other devices. As such, PLCs play a vital role in ensuring industrial automation systems’ smooth and efficient operation.
PLCs can be programmed to perform a variety of tasks, such as monitoring speeds and temperatures, controlling conveyor belts and valves, and managing safety systems. PLCs are designed to manage complex automation tasks, such as sequence control, motion control, and process control. In addition, PLCs can be used to monitor and optimize the performance of an industrial process. The main functions of a PLC include input/output handling, data storage and processing, and communication with other devices in the system. PLCs are highly versatile and can be programmed to perform a wide range of tasks. As a result, they are an essential part of any modern industrial automation system.
The future of PLCs in Industrial Automation Programmable logic controllers (PLCs) have been an essential part of industrial automation systems for many years. These rugged, compact devices are used to control and monitor a wide range of processes and machinery, from production line assembly robots to factory conveyor belts. As the demands of the industry continue to evolve, PLCs will likely play an even more important role in the future of industrial automation. For example, PLCs are increasingly being used in “smart” manufacturing applications, where they can be connected to sensors and other devices to collect data and make real-time decisions. This data-driven approach to manufacturing is expected to become more widespread in the years ahead, as companies look for ways to optimize production and improve efficiency. As industrial automation systems become more complex, PLCs will play an essential role in ensuring that everything runs smoothly.
A PLC can be programmed to turn on a motor when a sensor detects a certain level of pressure. PLCs can also be connected to other devices, such as sensors and HMIs, which allows them to collect data and provide information to operators. In the future, PLCs will continue to play an important role in industrial automation systems. They will become more intelligent and connected, allowing them to provide even better control and automation.
PLC Machines
The PLC has undergone several changes since it was first introduced in the late 19th century. Perhaps the most notable change is the switch from mechanical relays to electronic components. This change happened in the early 20th century and allowed for more compact and reliable PLCs. Another major change occurred in the mid-20th century with the introduction of microprocessors. This allowed PLCs to become more powerful and flexible, opening new applications for the technology. PLCs continue to evolve today, with ever more powerful processors and increasingly sophisticated software. As a result, PLC has come to play a vital role in modern industrial automation.
The most recent generation of PLCs includes several new features that make them more versatile and easier to use than ever before. One of the most notable new features is web-based programming, which allows users to program PLCs from anywhere in the world using a web browser. Another popular new feature is data logging, which allows PLCs to record data for later analysis. PLCs also now come with built-in Wi-Fi and Bluetooth connectivity, making it easy to connect them to other devices for monitoring and control. These are just a few of the many new features that have been added to PLCs in recent years, making them more capable and user-friendly than ever before.
Uses of PLC
A PLC, or programmable logic controller, is a sophisticated device that can be used to control a wide variety of machinery and processes. PLCs are commonly used in manufacturing and industrial settings, where they can be used to monitor and control conveyor belts, pumps, motors, and other equipment. PLCs are also increasingly being used in building automation systems, where they can be used to control HVAC systems, lighting, and security systems. In addition to their broad range of applications, PLCs offer several advantages over traditional mechanical controllers. PLCs are highly programmable and can be easily reconfigured to change the way they operate. They are also much more reliable than mechanical devices, which often break down or suffer from wear and tear. As a result, PLCs are an essential tool for anyone who needs to control complex machinery or processes.
Types of PLCs
There are several different types of PLCs, each with its own set of capabilities and features. Each type of PLC has its advantages and disadvantages, so it is important to choose the right type for the application.
1. Relay-type PLC:
As its name suggests, this type of PLC uses relays to control the process or machine. Relays are electric switches that can be turned on or off by an electric current. When a relay is turned on, it closes an electrical circuit, and when it is turned off, it opens the circuit. A relay-type PLC typically has several input and output ports, which are used to connect the PLC to the devices it is controlling. The input ports are used to receive signals from sensors, while the output ports are used to activate actuators. In addition, relay-type PLCs often have special ports for programming and monitoring purposes.
This type of PLC is well-suited for applications that require a high degree of accuracy and repeatability, such as manufacturing processes. Relay-type PLCs are also very rugged and can withstand harsh environments. One downside of this type of PLC is that it is not as fast as other types of PLCs, such as microprocessor-based PLCs. Another downside is that relay-type PLCs are not as easily expandable as other types of PLCs.
2. Ladder logic PLC:
This is a type of PLC that uses a set of instructions that are arranged in a ladder-like fashion. The PLC runs through these instructions sequentially, executing each instruction in turn. Ladder logic is a programming language used to create programs for programmable logic controllers (PLCs). It is based on the rungs of a ladder, with each rung representing a certain instruction or set of instructions. Ladder logic is one of the most popular PLC programming languages because it is easy to learn and use. In addition, ladder logic programs can be easily converted into other programming languages, making it a versatile tool for PLC programmers.
Ladder logic PLCs are well suited for simple applications that do not require complex processing. However, they can also be used for more sophisticated applications if the instructions are carefully designed. One advantage of ladder logic PLCs is that they are easy to program and debug. Another advantage is that they are often less expensive than other types of PLCs. One disadvantage is that they may not be able to handle complex applications as well as other types of PLCs.
3. Microprocessor-based PLC
Microprocessor-based PLCs are PLCs that use a microprocessor as their central processing unit. With a microprocessor-based PLC, it is possible to implement complex algorithms and control strategies that would be difficult or impossible to implement with a relay-based PLC. Microprocessor-based PLCs are more capable than older relay-type PLCs, and they can be programmed to perform complex tasks. They typically have an onboard microprocessor, memory, input/output (I/O) ports, and one or more communication ports. The microprocessor executes the stored program, which can be written in ladder logic or other languages.
Microprocessor-based PLCs are used in a wide range of industries, including manufacturing, food and beverage processing, packaging, oil and gas, power generation, and transportation. They are more flexible and can be programmed to perform more complex tasks. In addition, they are much smaller and more energy efficient. However, microprocessor-based PLCs are more expensive than relay-based PLCs and can be more difficult to troubleshoot. In addition, they are not as widely available as relay-based PLCs.
The Programmable Logic Controller, or PLC, has been a staple of industrial automation for many years. Its simple design and rugged construction make it ideal for use in harsh environments, and its ease of programming means that it can be quickly adapted to new `applications. Although PLC operates smartly to streamline industrial processes, it is now facing increased competition from newer technologies such as the Internet of Things (IoT) and artificial intelligence (AI). Messung is the most reliable PLC manufacturing company in India and we do not shy away from evolving with time. The industrial Internet of Things (IIoT) is transforming the manufacturing sector, and Messung PLCs are at the forefront of this revolution. These next-generation controller platforms are designed to future-proof, with the flexibility to scale up or down as needed.
As the leading company among PLC manufacturers in India, we at Messung understand the importance of keeping your business running smoothly and our products reflect that commitment. The benefits of using Messung PLC systems for industrial automation are clear. They provide a high degree of reliability, durability, and safety. In addition, they offer an intuitive user interface that makes them easy to learn and operate. With all these features and benefits, it’s no wonder that Messung PLC systems are the preferred choice for so many businesses worldwide. If you’re looking for a dependable PLC system that will make your industrial automation processes more seamless, Messung has the perfect automation solution for you.