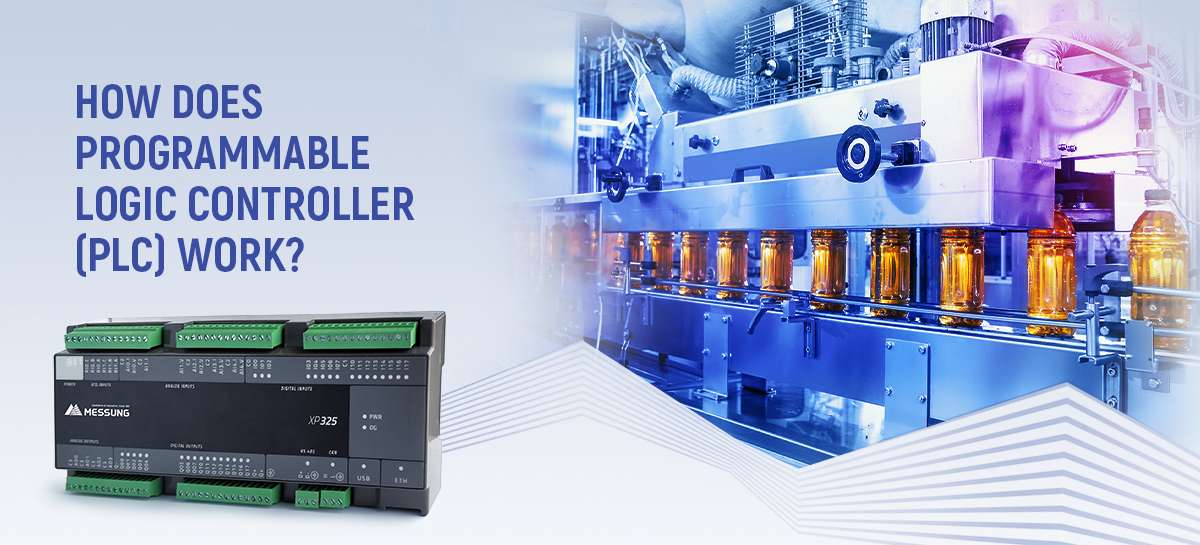
Introduced in the early 1970s, Programmable Logic Controller (PLC) have come a long way and are easily one of the most important industrial automation technologies today. The widespread use of PLCs in factories and other industrial settings is a result of its ability to control and monitor manufacturing processes.
PLCs are a crucial component in industrial process automation. It operates on instructions that are stored in a memory module, which can include both program instructions and data. It takes input from sensors and performs logical operations on that data to produce the desired output.
Let’s understand the PLC a little better
1. What is PLC ?
A programmable logic controller, or PLC, is a special-purpose computer used to control industrial processes and machinery. Bloomberg defines a PLC as “a digital computer that performs logical operations on input data, usually controlling electromechanical processes such as those in factories and utilities.”
The important thing to understand is that a PLC is a type of digital computer that makes other devices work smoothly by performing logical operations on input data. It is essentially like a tiny brain for industrial automatics and machines. PLCs are widely used in industry to automate the sequential operation of machines and processes.
So how does a PLC work? In this article, we will take a closer look at the basics of how this device operates.
2. The PLC Process
Programmable Logic Controllers (PLCs) are used to control actuators, motors, valves, sequence machines and other devices in an industrial process.
In general, PLCs operate by receiving input from sensors and then using that information to control various devices or processes. For example, a PLC might be used to control the operation of a conveyor belt. PLCs typically have several input and output ports that can be easily configured to meet the specific needs of a given application. PLCs are widely used in industrial settings due to their versatility and ease of use.
3. The PLC System
A PLC is made up of five components: power supply, the processor, communication card, input modules, and output modules.
The input module receives input signals from switches, sensors or other devices while the output module sends control signals to actuators or other devices. The processor reads Ladder Logic programs from memory and executes them to control the process. PLCs come in different sizes and configurations depending on the application requirements. They can be programmed to perform various tasks depending on the need.
4. How PLC Operates
Operationally, a PLC is very similar to a computer. It has a CPU, or central processing unit, which executes the program that has been loaded into memory. The memory can be either volatile or non-volatile, meaning that it can retain the program even when power is shut off. In addition to the CPU and memory, a PLC also has input/output (I/O) modules.
Input/output (I/O) modules are a critical component of automation technology, and PLC manufacturers in India offer a wide variety of options for customers to choose from. I/O modules convert the analog signals from sensors and other devices into digital signals that can be processed by the PLC, and they also convert the digital signals output by the PLC into analog signals that can be used by actuators and other devices.
In addition to offering a variety of different I/O modules, PLC manufacturers in India also provide customization services to meet the specific needs of their customers. As a result, automation technology customers have access to a wide range of PLC input/output modules that can meet their specific requirements.
These modules allow the PLC to interact with the outside world, receiving input signals and sending out output signals. The I/O modules are typically connected to sensors and actuators, which are devices that detect or cause physical changes.
5. Advantages of using a PLC in manufacturing
Automation technology has revolutionized the manufacturing process by making it more efficient and cost-effective. PLC input-output modules are an important part of this automation technology.
PLC manufacturers in India offer a wide range of input-output modules that are designed to meet the specific needs of the manufacturing process. These modules help to automate the process by providing an interface between the various input and output devices. The main advantage PLCs offer to industrial automation is reliability. By reducing the need for manual intervention which is liable to human errors, PLCs ensure efficiency in performance. In addition, they also provide flexibility, low cost output, faster response time and easy troubleshooting. As a result, PLCs can play a vital role in improving the overall manufacturing process.
6. Applications of PLCs in Various Industries
PLCs are designed to be highly versatile and can be programmed to perform a wide range of tasks. These compact computers are used to control industrial processes. PLCs can be used to control a wide range of equipment, from conveyor belts to machine tools.
PLCs are used extensively in the automotive and textile industries. They are also becoming increasingly popular in the food and beverage industry. PLCs offer many advantages over traditional mechanical control systems. They are more compact, more reliable, and easier to program. Additionally, PLCs can be connected to a network of other devices, making it possible to remotely monitor and control industrial processes. As a result, PLCs are playing an increasingly important role in industrial automatics.
7. Recent developments in PLC technology
While PLCs were once only used in large industrial applications, they are now commonly used in smaller scale applications such as home automation. There are many PLC manufacturers in India, manufacturing compact PLCs which are becoming increasingly popular due to their flexibility and affordability.
A compact PLC is small in size and offers many benefits over larger PLCs. One advantage of using a compact PLC is that it requires less wiring. This is because the compact PLC uses smaller input/output modules that are mounted on DIN rails. This reduces the amount of wiring that is required, making installation quicker and easier.
Another advantage of using a compact PLC is that it consumes less power. This is because compact PLCs use fewer components than larger PLCs. As a result, they are more energy-efficient and can help to lower your energy bills. Finally, compact PLCs are often less expensive than larger PLCs. This makes them an excellent choice for smaller applications and budget-conscious manufacturers.
8. Messung PLCs
Messung’s advanced PLCs can control complex industrial processes, machines and high-performance production lines. Made modern, sleek and fast, Messung bases its PLC systems on cutting-edge technology that ensure reliable performance along with extra perks such as smooth connectivity to the cloud and IoT functionalities which keep your business’s productive growth rising steadily.
Messung’s industry processes automation & control solutions manage highly complex projects for productive efficiency and high availability and contribute towards building a strong infrastructure for safe and efficient operations from source to consumer. We automate and modernise the most complex systems and offer a wide range of products and services for systems integration.
At Messung, experienced engineers develop industrial automation products honing the latest technology and utilizing extensive industry expertise to partner with your industry. We not only understand your needs and challenges to develop machine automation and industrial automation solutions that are suitable for your application but also offer future conscious service that evolves with your changing dynamics. Trust Messung to take your industrial automation to the next level.